汽车充电口盖作为电动汽车的重要外饰部件,其材料选择需要综合考量功能性、耐用性、轻量化及成本等多重因素。目前市场上主流的充电口盖材料主要包括以下三类:
### 一、工程塑料(占比约70%)
聚(PP)和-丁二烯-共聚物(ABS)是应用广泛的材料。PP材料具有优异的耐化学腐蚀性,可承受-30℃至100℃的温度范围,且密度仅为0.9g/cm3,能有效降低车身重量。ABS则凭借更高的表面光洁度和尺寸稳定性,常用于车型。例如特斯拉Model 3采用改性PP材料,通过添加玻璃纤维增强后,其抗冲击强度可达80kJ/m2。塑料件普遍采用注塑成型工艺,单件成本可控制在20-50元。
### 二、金属材料(占比约25%)
铝合金(6061-T6)和不锈钢(304/316L)主要应用于豪华车型。铝合金充电口盖经阳氧化处理后,表面硬度可达HV200以上,同时保持1.2-1.5mm的轻量化壁厚。保时捷Taycan采用的锻造铝合金盖板,重量比钢制件减轻40%,但成本高达300-500元/件。金属材料需进行盐雾测试(500小时无腐蚀),并配备电磁屏蔽层以满足EMC要求。
### 三、复合材料(占比约5%)
碳纤维增强聚合物(CFRP)和玻璃纤维复合材料(GFRP)逐步应用于超跑领域。宝马i8采用的CFRP充电盖板,拉伸强度达到1500MPa,厚度仅1.8mm,但制造成本是塑料件的10倍以上。新兴的生物基复合材料(如麻纤维增强PLA)也开始试产,其碳排放量比传统塑料降低30%。
材料发展趋势呈现明显分化:经济型车持续优化塑料改性技术,中端车型探索塑料/金属复合结构,产品则向智能材料演进。研发的自修复聚氨酯涂层技术,可在40℃下2小时内修复0.3mm划痕,或将下一代充电口盖的革新。材料选择需平衡性能指标与成本控制,同时满足UL94 V-0阻燃标准和RoHS环保指令,这成为车企供应链管理的重要课题。
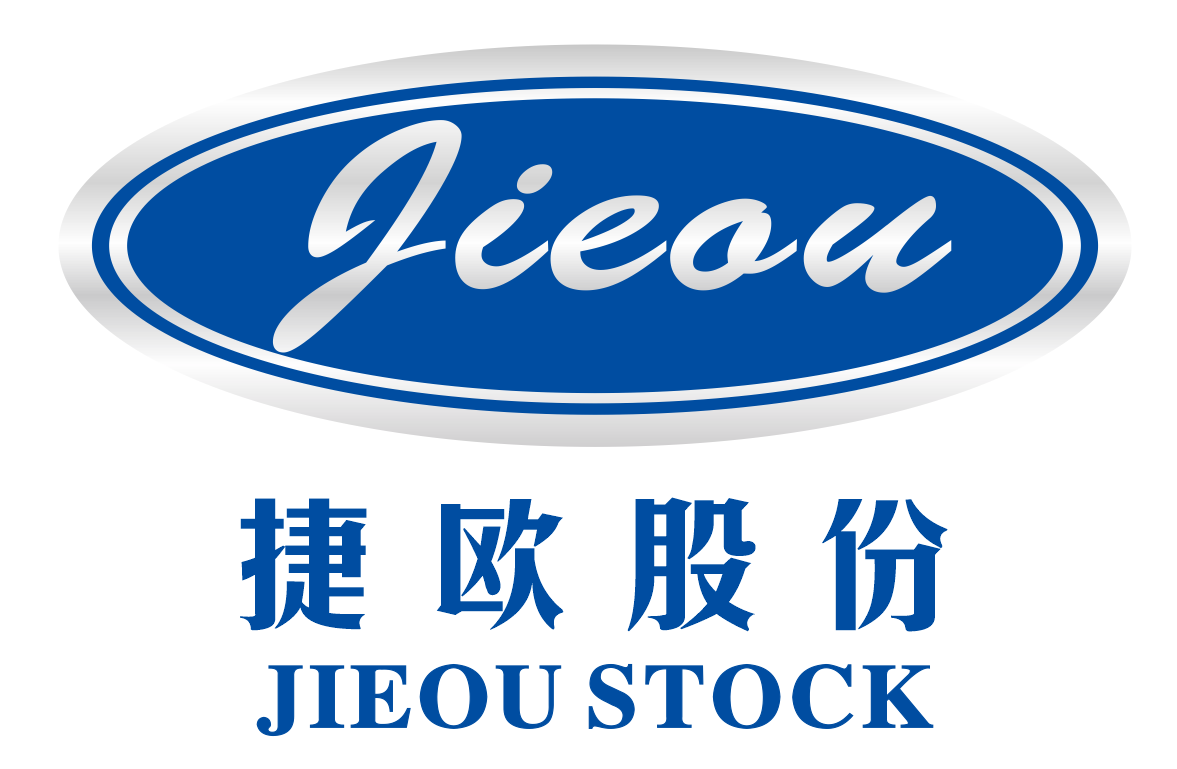