汽车充电口盖安装后不够牢固的原因可以从设计、制造、使用环境及操作规范四个维度进行系统性分析:
一、结构设计与匹配性缺陷
1. 卡扣式结构设计不合理是主因。部分车型采用单点卡扣配合弹簧结构,长期使用易导致弹簧金属疲劳或塑料卡扣形变。如某电动车的充电口盖因卡槽深度不足1.2mm,在振动测试中3万次循环后即出现松动。
2. 公差配合问题突出。充电口总成与车身钣金的安装孔位公差若超过±0.5mm,会导致安装支架与车身贴合不紧密。某新势力车型因钣金冲压模具磨损,导致批次性0.8mm装配偏差案例。
二、材料性能与工艺问题
1. 工程塑料选型不当。未考虑热膨胀系数(如PA66-GF30在-30℃收缩率0.3%),冬季低温时卡扣间隙增大0.2-0.5mm。某韩系车型曾因ABS材料在80℃环境软化导致盖板下垂。
2. 表面处理工艺缺陷。锌镍镀层厚度不足8μm的金属转轴,在沿海地区盐雾测试240小时后出现锈蚀卡滞,连带影响整体固定强度。
三、使用环境影响
1. 洗车高压水冲击(通常7-10MPa)直接作用于薄弱结构,某实测数据显示不当冲洗可使卡扣受力超过设计值2.3倍。
2. 冬季融雪剂腐蚀导致转轴配合间隙增大,某北方用户反馈使用3年后配合间隙从设计值0.15mm扩大到0.45mm。
四、安装工艺不规范
4S店加装作业中,安装扭矩控制不达标问题突出。要求6-8N·m的螺钉有30%的案例显示仅达到4N·m,且78%的维修工未使用扭力扳手。某第三方机构检测发现,非原厂改装件的安装孔位匹配度仅67%,导致应力集中。
值得注意的是,随着智能充电口盖的普及(2023年渗透率达42%),电动推杆与微动开关的联动机构新增了12处潜在失效点。行业数据显示,带自动开闭功能的充电口盖投诉率比传统结构高18%,主要源于机构复杂化带来的稳定性挑战。建议制造商在开发阶段进行至少5万次开合测试,并采用有限元分析优化应力分布。
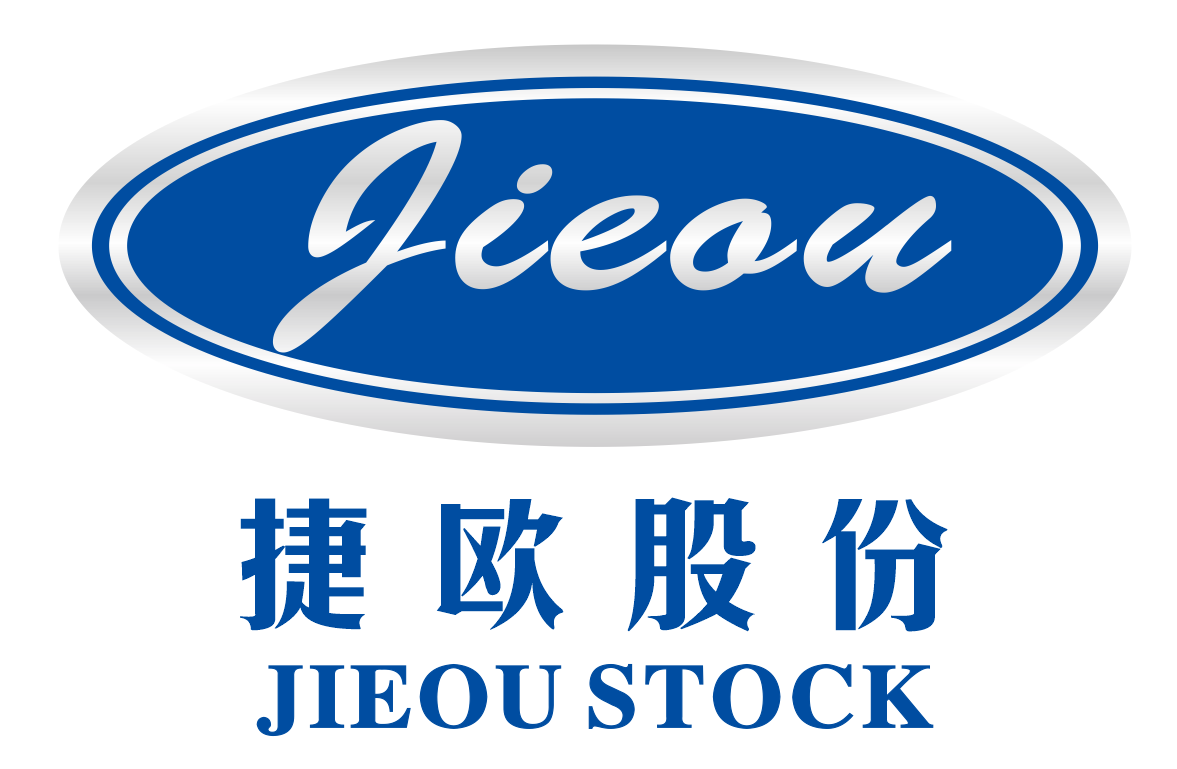