汽车充电口盖作为电动汽车充电系统的重要防护部件,其高温环境下的性能表现直接关系到充电安全性与设备耐久性。以下从材料特性、结构设计、密封性能及安全测试等方面进行分析:
**1. 材料耐温性与稳定性**
充电口盖多采用工程塑料(如PA66-GF30、PC/ABS合金)或复合材料制造,这类材料通常具备120℃-150℃的短期耐热能力。在50℃-80℃的常规高温环境中,材料力学性能保持率可达90%以上,但在持续暴晒下,部分材料可能出现表面粉化或轻微形变。车型会采用添加耐候剂的特种塑料,可在85℃环境下保持2000小时以上的尺寸稳定性。
**2. 结构设计优化**
双锁扣结构和弹簧铰链设计能有效应对热胀冷缩影响。实验数据显示,在70℃高温箱中测试时,采用金属嵌件加强的卡扣结构,其开合力衰减幅度较全塑结构降低40%。部分引入气隙导流设计,使充电口内部温度较外部降低8-12℃,避免热量积聚。
**3. 密封系统可靠性**
硅橡胶密封圈在120℃高温下仍能保持70%以上的压缩回弹率,优于传统EPDM橡胶。IP54/IP67防护等级测试表明,在85℃高温高湿(95%RH)环境中,密封系统可维持48小时无渗水。但长期高温可能加速密封圈老化,建议每2年进密性检测。
**4. 安全测试标准**
行业普遍采用ISO 20653:2013标准,要求充电口盖在-40℃至+85℃温度循环测试后,仍能承受10N·m的冲击测试。实际道路测试显示,沙漠地区车辆充电口盖表面温度可达92℃,此时应避免立即进行大电流快充,待温度降至65℃以下为宜。
建议用户定期清洁充电口盖散热格栅,避免异物阻塞影响散热。制造商则需重点优化高温区域的材料厚度分布,采用模流分析预防热变形。随着800V高压快充技术的普及,充电口盖的耐高温性能标准将进一步提升至100℃工况要求。
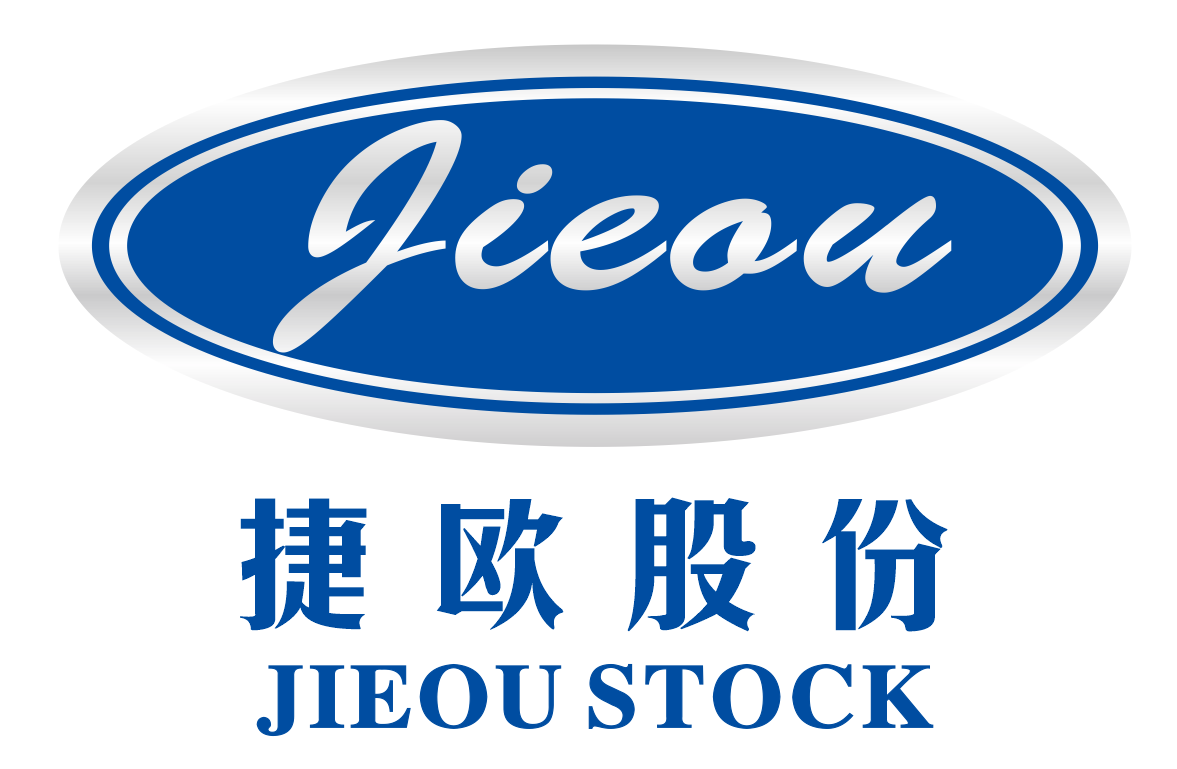